Pump body
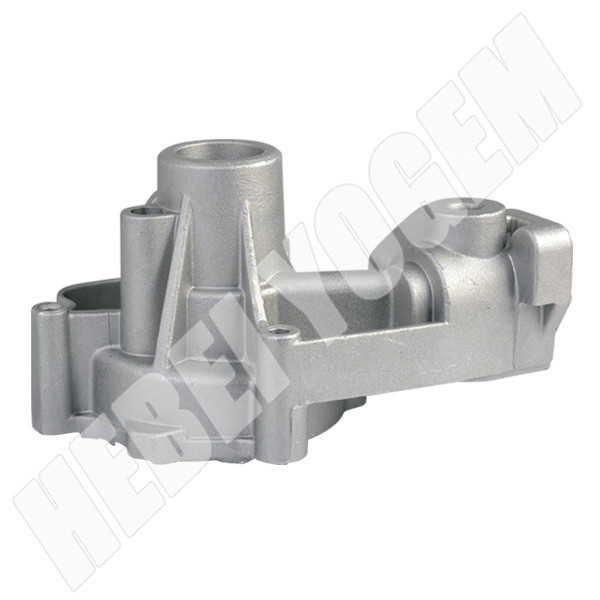
technology:Sand casting, die casting, gravity casting, investment casting
application:Pump, valve, automobile, agriculture, other mechanical field.
Aluminum casting
Aluminum castings are formed by pouring molten metal into molds which have been shaped by a pattern of the desired product. Three common types of molding methods are used to produce aluminum castings:
Die casting
Die casting uses pressure to force molten aluminum into a steel die (mold). This type of casting is often used for mass production of parts, which require a minimum amount of finishing and machining. Die casting has short cycle times but high costs for tooling. The pressurized casting system creates a high strength skin but weaker interior than permanent mold casting.
Permanent mold casting
Permanent mold casting uses steel (or other metal) molds and cores. Strong castings are formed by pouring aluminum into the mold. Permanent molds are used to create highly repeatable parts with consistency. Their rapid cooling rates generate a more consistent microstructure, which can improve the mechanical properties significantly.
Sand casting
Sand castings are created by packing a fine sand mixture around a pattern of the desired product. The pattern is slightly larger than the final product to allow for shrinkage of the aluminum while cooling. Sand casting is economical because the sand is reused multiple times over. It is also effective for creating large moldings or moldings with detailed designs. Upfront tooling costs are low but per part prices are higher, making sand casting more suitable for specialized castings than mass production.